3D Printed Wings: Revolutionizing the Future of Flight
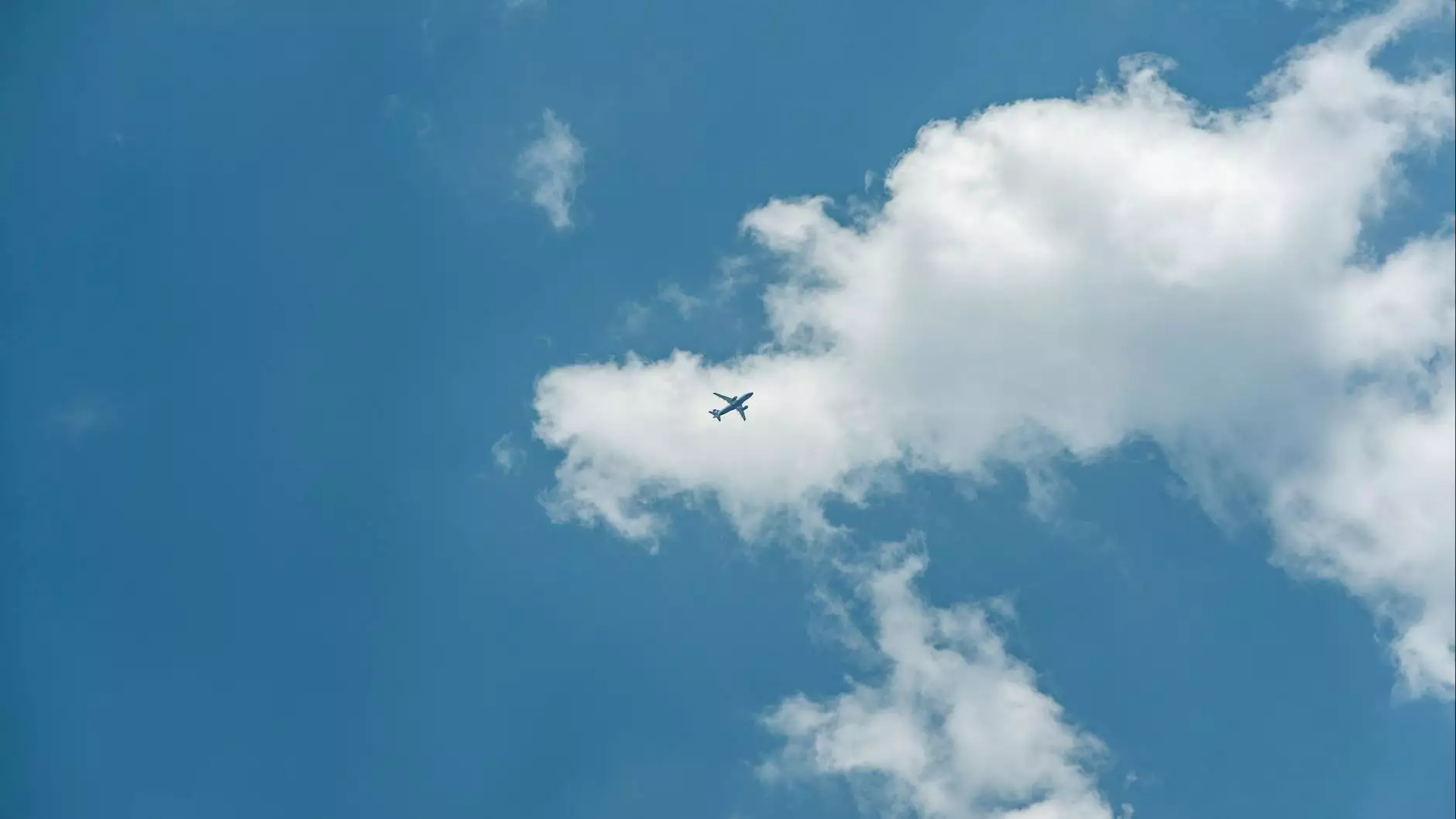
In recent years, the aviation industry has witnessed a remarkable transformation, thanks to emerging technologies such as 3D printing. One of the most innovative applications of this technology is the production of 3D printed wings. This article delves into the intricate world of 3D printed wings, exploring how they are reshaping the aviation landscape and offering enhanced performance, sustainability, and design possibilities.
The Basics of 3D Printing in Aviation
Before diving into the specific advantages of 3D printed wings, it's essential to understand how 3D printing is integrated into the aviation sector. 3D printing, also known as additive manufacturing, involves creating three-dimensional objects layer by layer from a digital file. This technology allows for incredible design flexibility, enabling engineers to produce complex geometries that would be nearly impossible to achieve using traditional manufacturing methods.
Innovative Design Possibilities with 3D Printed Wings
One of the most significant advantages of 3D printed wings is the unprecedented design capabilities that come with additive manufacturing. Here are some key points regarding design flexibility:
- Complex Geometries: Traditional wing designs often require extensive modifications to achieve desired aerodynamic properties. However, with 3D printing, designers can create complex shapes that optimize aerodynamics, leading to improved lift and reduced drag.
- Lightweight Structures: One of the primary goals in aviation design is to reduce weight. 3D printed wings can be made significantly lighter without sacrificing strength, using advanced materials that are both durable and lightweight.
- Customization: The ability to customize designs for specific applications is a game-changer. Airlines can create tailored wings suited for different routes or environmental conditions, enhancing overall performance.
- Rapid Prototyping: The speed at which designs can be modified and printed allows for rapid prototyping. Engineers can iteratively test and improve wing designs without the long lead times associated with traditional manufacturing.
Advantages of 3D Printed Wings in Aircraft Performance
The integration of 3D printed wings not only enhances design but also translates into improved performance across several parameters:
- Enhanced Aerodynamic Efficiency: The intricate designs achievable through 3D printing lead to improved airflow over the wings, resulting in enhanced lift-to-drag ratios.
- Fuel Efficiency: By reducing weight and optimizing shape, 3D printed wings contribute to lower fuel consumption, which is crucial for airlines aiming to cut operational costs and reduce their carbon footprint.
- Improved Structural Integrity: 3D printing allows for the use of advanced composite materials that can withstand varied stressors, enhancing the longevity of wings and reducing maintenance costs.
- Adaptability: As technology evolves, so too can wing designs. The ability to adapt and upgrade wing designs easily means that aircraft can continually enhance their performance without complete overhauls.
Sustainability in Aviation through 3D Printed Wings
As the aviation industry faces growing pressure to reduce its environmental impact, 3D printed wings offer a promising avenue towards sustainability. Here are several ways in which this technology contributes to greener aviation:
- Material Efficiency: Traditional manufacturing often leads to significant waste. 3D printing minimizes this waste by using only the necessary amount of material, significantly reducing the environmental impact.
- Localized Production: 3D printing allows components to be produced closer to where they are needed, reducing transportation emissions and associated costs.
- Recyclable Materials: Many materials used in 3D printing are recyclable, which adds another layer of sustainability by allowing for end-of-life recycling of aircraft parts.
Case Studies: Successful Implementations of 3D Printed Wings
To illustrate the real-world impact of 3D printed wings, let’s examine a few prominent case studies within the aviation industry:
Case Study 1: Airbus and its A320 Wing Component
Airbus has been a pioneer in the integration of 3D printing technologies, investing in additive manufacturing for producing lightweight wing components. A notable achievement was the successful creation of a 3D printed wing tip for the A320 family, which not only reduced weight but also proved to enhance aerodynamics and fuel efficiency.
Case Study 2: Boeing’s Innovative Approaches
Boeing has leveraged 3D printing to develop various components of their aircraft, including lightweight wing structures. By utilizing advanced polymers and composites, they have successfully produced parts that significantly enhance structural performance while remaining cost-effective.
Case Study 3: MIT’s Wing Design
The Massachusetts Institute of Technology (MIT) has conducted extensive research in 3D printing for aviation applications, specifically focusing on wing design. Their innovative research has led to the creation of prototypes that demonstrate superior performance metrics, setting a benchmark for future developments in wing technology.
Challenges in Implementing 3D Printed Wings
While the potential advantages of 3D printed wings are significant, it is essential to acknowledge the challenges that manufacturers face in implementing this technology:
- Regulatory Hurdles: The aviation industry is heavily regulated. Gaining approval for new materials and manufacturing processes can be time-consuming and complex.
- Material Limitations: While advancements are being made, not all 3D printing materials are suitable for the demanding environment of aviation. Research is ongoing to develop materials that meet regulatory standards and performance expectations.
- Cost Implications: Although 3D printing can reduce costs in the long run, the initial investment in technology and training can be substantial, posing a barrier for some manufacturers.
The Future of 3D Printed Wings in Aviation
The future of 3D printed wings in aviation appears promising, with ongoing research and development aimed at overcoming existing challenges. As the technology matures, we can anticipate several exciting advancements:
- Integration of AI and Machine Learning: The use of AI in the design and testing phases will likely accelerate the production of high-performance wing designs that are optimized for specific conditions.
- Increased Adoption by Major Airlines: As the benefits become more evident, it is expected that more airlines will adopt 3D printed wings as part of their standard fleet configurations.
- Advanced Materials Development: Continued research in materials science will lead to new composites that can withstand the exigencies of flight while being lightweight and cost-effective.
- Global Collaboration: The aviation industry will likely see increased collaboration across borders, with companies sharing knowledge and innovations in 3D printing technologies.
Conclusion: The Impact of 3D Printed Wings on the Aviation Industry
The advent of 3D printed wings is more than just a trend; it is a transformative force in the aviation landscape. By enabling innovative designs, enhancing performance, and promoting sustainability, 3D printed wings are setting a new standard in aircraft manufacturing. As the industry continues to adapt and grow, the potential for 3D printing will only expand, leading to exciting developments in the future of flight. Embracing this technology will not only benefit manufacturers but will also pave the way for a greener and more efficient aviation sector.
By investing in 3D printed wings, companies can position themselves at the forefront of the aviation revolution, ensuring they are part of a future that is not only innovative but also sustainable.